Types of Plastic Overview
What are the Materials Used in Plastic Injection Molding?
Injection molding is considered to be one of the fastest and most optimized methods of producing large numbers of identical plastic components at one time. Injection molding is used for nearly every consumer plastic product and is the most common plastic manufacturing method around. Because of the wide range of applications and industries where plastics are used, different chemical formulations are required for the plastic injection molding process.
The professionals at Retlaw Industries use a wide variety of plastics when manufacturing our molded products, depending on what type of plastic product our customers need.
Our expert plastic part designers will work on your new or existing design concept to find the best material for your particular application. Whether you need electronic enclosures molded from ABS or pull-out drawer handles made from acetal (POM), our experts will address your needs and help you build the best part possible out of the best materials available.
Contact Retlaw Industries Today
Here are some of the plastic materials our experts use in plastic injection molding:
Acrylic (PMMA)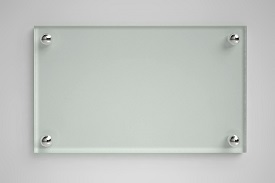
Also known as Plexiglas, acrylic is a hard transparent plastic material often used in electronics and automotive parts. Other forms of acrylic are also used in everyday products due to its natural transparency and coloring properties, everything from eyewear lenses, acrylic paint, and even acrylic nails. Acrylic can also be colorized to be either translucent or opaque.
In commercial applications, acrylic falls under #7 (OTHER). This can include other types of plastics including polycarbonate, polylactic fibers, nylon, and fiberglass.
Advantages of Acrylic:
- Transparency – among the clearest plastics available today
- Weather Resistance – resists moisture and ultraviolet discoloration
- Chemical Resistance – unaffected by water and weak acids and alkaline solutions
- Surface Hardness – good impact strength and rigidity
- Dimensional Stability – lends to a predictable final product
Acrylonitrile Butadiene Styrene (ABS)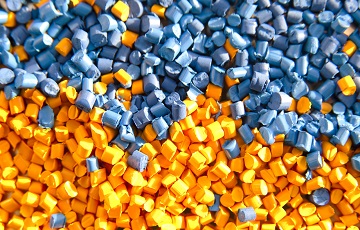
ABS plastic is one of the most commonly used plastics in injection molding due to its wide temperature range, good stability, and insulating properties. ABS is commonly found in plastic toys such as Lego bricks, but it’s also often used in many types of electronics, tools, and home repair equipment.
Advantages of ABS:
- Impact Resistance – rubberlike formulations make ABS resilient to impact
- Surface hardness – high rigidity in certain formulations
- Chemical Resistance – not affected by alkalis, water, and most inorganic acids
- Uniform Shrinkage – good dimensional stability
- Wide Temperature Range – resists heat and won’t shatter in cold
- Machinability – easy to form after cooling
High-Density Polyethylene (HDPE)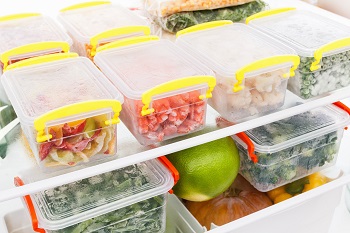
When in need of rigid, heat-resistant plastic, HDPE is the best material to use. Since polyethylene is a food-grade plastic – meaning it is safe to use around food – this material is commonly manufactured in storage containers, kitchenware, and refrigerator shelving. HDPE is also a good plastic for holding chemical-based products such as cleaning agents, laundry detergent, bleach, and shampoo.
In commercial applications, HDPE falls under #2 (HDPE).
Advantages of HDPE:
- Sustainable – made of 100% recyclable material
- Chemical Resistance – resistant to corrosion, rust, and other chemicals
- Heat Resistance – doesn’t melt or corrode in high temperatures
- Food Grade – safe to use as food packaging and equipment
- Inexpensive – can be mass-produced at a low price
Nylon (PA)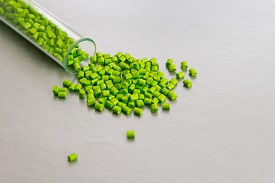
Nylon is one of the most versatile materials used in plastic injection molding. It’s commonly combined with a range of other materials to enhance its characteristics. Thanks to its high melting temperature and low friction properties, it’s useful for a wide range of products such as nylon rope, reinforced automotive parts, and even clothing.
Advantages of Nylon:
- Low Friction – doesn’t heat up under high friction
- Chemical Resistance – resistant to corrosion from chemicals
- Abrasion Resistance – useful for elastic and clothing applications
- Adaptable – can be combined with many other types of plastic materials
Polycarbonate (PC)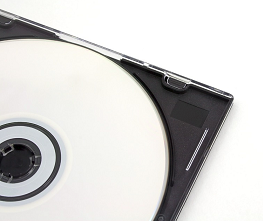
Polycarbonate is a useful plastic material for applications needing transparency or high impact resistance. For this reason, polycarbonate is most commonly used in eyewear applications, but it’s also used in pipes for LED lights, clear windows, and sporting equipment.
In commercial applications, polycarbonate falls under #7 (OTHER). This can include other types of plastics including acrylic, polylactic fibers, nylon, and fiberglass.
Advantages of Polycarbonate:
- Impact Resistance – doesn’t scratch or dent under impact
- UV Resistance – doesn’t corrode or discolor in ultraviolet light
- Transparency – can be made into windows and eyewear lenses
- Chemical Resistance – doesn’t corrode from chemicals
- Rigidity – makes for good eyewear and window applications
Polyetherimide (PEI)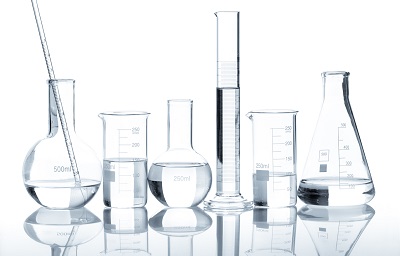
Polyetherimide, also known as Ultem, is an amorphous material with extremely high heat resistance compared to other plastics. Due to its rigidity and high heat performance, polyetherimide is most commonly used in medical devices, electronics, and industrial plastic parts.
Advantages of Polyetherimide:
- Rigidity – hard plastic useful for high-impact industrial applications
- Heat Resistance – doesn’t melt or warp under high temperatures
- High Tensile Strength – resists cracking or breaking in hard environmental conditions
- Flame Resistance – isn’t flammable and generates low smoke
Polyoxymethylene (POM)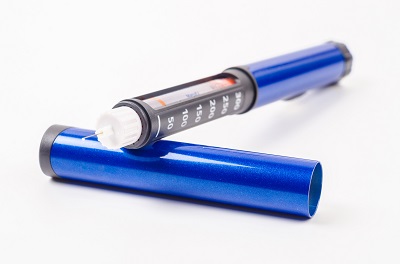
Also known as Acetal, polyoxymethylene is a semi-crystalline polymer which is very rigid and has a naturally glossy surface, making it a useful material for a wide range of industries. Acetal is most commonly found in automotive applications, household appliances, and electronics.
Advantages of Polyoxymethylene:
- Rigidity – stays strong and doesn’t bend easily
- Impact Resistance – strong and stable enough to resist strong impacts
- Solvent Resistance – doesn’t corrode or rust due to chemicals and solvents
- Glossy surface – smooth, reflective properties
Polypropylene (PP)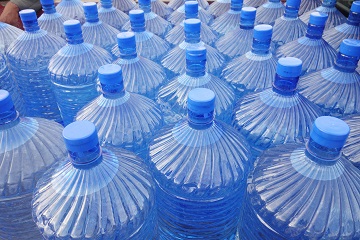
Much like Acetal, polypropylene is a plastic with a naturally glossy surface when properly manufactured. Its chemical resistance and elastic properties make it useful for a wide variety of food-related applications, including plastic kitchenware, dishwasher-safe plates, and storage containers. Polypropylene is also commonly used to make toys, hard luggage containers, and even external car parts.
In commercial applications, polypropylene falls under #5 (PP).
Advantages of Polypropylene:
- Chemical Resistance – doesn’t react with most bases and acids
- Fatigue Resistance – retains its shape after a lot of bending and flexing
- Electrical Resistance – strong insulation properties
- Elasticity – can bend, flex and deform without actually breaking
Polystyrene (PS)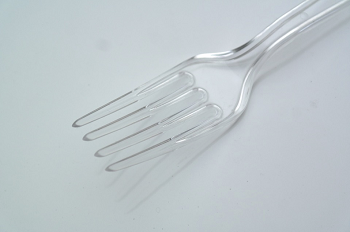
Polystyrene is a polymer used in a wide variety of plastic and foam applications across a range of industries. Due to its bending and flexing properties, polystyrene is often used in hinged applications, such as disposable food containers and bottles. It’s also widely used to make rigid foam insulation and sheeting for laminate floors.
In commercial applications, polystyrene falls under #6 (PS).
Advantages of Polystyrene:
- Optical Clarity – transparent resin can be useful for see-through plastic products
- FDA Grade – safe to use when packaging food and consumable materials
- Stability – rigid material useful for packaging
- Inexpensive – can be mass-produced at a low cost