Common Defects with Plastic Injection Molding and How to Avoid Them
Sink Marks
Depressions can form in certain areas of a plastic molded part. They’re usually caused when the cooling device is insufficient and doesn’t fully cure the product. They can also be caused by inadequate pressure in the mold cavity – if different sections of the molded part have varying degrees of thickness, then those parts are more likely to have sink marks.
These defects can be harmful to the structural integrity of the plastic part and make it unusable for production applications.
-
How to Avoid: Mold temperatures should be lowered while cooling time prolonged to allow for more adequate curing of the plastic molded part.
Bubbles
Bubbles, also known as vacuum voids, are pockets of air trapped within a plastic part, usually close to the surface. They’re usually caused by uneven or insufficient holding pressure inside the plastic mold which doesn’t properly condense the molten plastic so every space is filled. Bubbles can also form when two halves of a mold come together and don’t align properly.
-
How to Avoid: There are several ways to avoid bubbles: one way is to switch to a melted plastic with a lower viscosity, making it less likely to have air bubbles get trapped inside the plastic. Other ways to avoid bubbles forming would be to increase the holding pressure inside the mold and to take extra care to ensure the two mold halves are aligned.
Surface Delamination
Delamination occurs when thin layers on the surface of a plastic part appear and peel off piece by piece. This occurs usually because of contaminated foreign materials finding their way into the molten plastic, affecting the finished product by not allowing the plastic to bond properly. Foreign materials can include anything from water to the mold release agent used during the plastic molding process.
-
How to Avoid: Don’t use too much mold release agent when demolding the plastic component. If there’s an issue with the demolding process, you may need to repair the ejection system or whatever other underlying issues there may be.
Warping
Also known as warpage, warping is deformation and uneven shrinkage in different parts of the molded component. This usually occurs when there’s non-uniform cooling of the plastic material, causing different parts of the plastic part to cool at different rates. The internal stresses of the uneven plastic material lead to a twisted, uneven shape.
-
How to Avoid: Ensure sufficiently long cooling times to avoid residual stresses and deformations. Also, be sure to design the mold with uniform wall thickness so the plastic cools evenly.
Jetting
This occurs when molten plastic fails to stick to the mold surface due to the speed of the injection. When melted plastic has a viscosity which is too high, it’s rapidly cooled when it hits the mold, and the viscosity increases, leaving marks on the surface of the finished product.
-
How to Avoid: Increase the mold and melt temperatures to avoid raising the viscosity of the molten plastic. Also, increase the size of the gate so the injection speed becomes slower.
Flow Lines
Flow lines are discolored lines that show up on a prototype part. These lines are a result of how the molten plastic cools as it flows into the mold cavity, such as if the speed varies too much, the mold’s wall thicknesses vary too much, or the flow changes directions as the cavity bends and contours. Flow lines usually happen when the injection speed is too low, causing the plastic to solidify far too soon.
-
How to Avoid: Increase injection molding speeds and pressure levels, and ensure the cavities are filled properly so that they cool evenly. If the wall thicknesses change, round the corners in the direction of the injection flow.
Burn Marks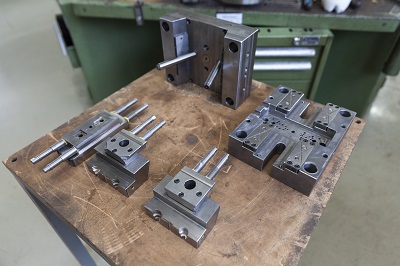
Burn marks are typically black or brown-colored discolorations on an edge or surface of a molded plastic component. Burn marks generally don’t affect part integrity, unless the plastic is burned to the extent of degradation. Burns are usually caused by trapped air overheating in the mold cavity.
-
How to Avoid: lower the melt and mold temperature to prevent the part from overheating, and reduce the injection speed to limit the risk of trapping air inside the mold.
Weld Lines
Weld lines can appear on the surface of a molded part where the molten material has converged after splitting off in a mold. The thin weld line is the result of weak material bonding, which lowers the strength of the part. The part becomes partially solidified and won’t sufficiently bond where the two halves meet, resulting in weld lines.
-
How to Avoid: Increase material temperature to prevent partial or uneven solidification, and raise injection speed to limit cooling.
Discoloration
Discoloration, also known as “color streaking”, occurs when a plastic part is a different color than intended. Often the discoloration is limited to a localized area or a few streaks of abnormal color on a molded part. A common cause of discoloration is leftover pellets in the hopper or residual resin in the nozzle or mold from a previous production run.
-
How to Avoid: Ensure that you properly clean the hopper, nozzle, and mold between production runs to eliminate any residual materials.
Need high-quality plastic injection molding services to ensure your parts are made perfectly and without defects? Call the plastic molding professionals at Retlaw Industries today to get a product quote for idler pulleys, sprockets, rebar chairs, adapters, custom products, and more!